Effiziente Separation von Material
Problemstellungen in der Teileseparation
-
Die nachgeschaltete Separierung von Nutzteil und Anguss ist in der Spritzguss- und Druckgussproduktion oftmals im Produktionsprozess erforderlich
-
Eine Angussentnahme direkt im Werkzeug, z.B. durch Angusspicker, bedeutet verlängerte Zykluszeiten von bis zu 20%
-
Vorhandene Separiergeräte werden oft nicht mit optimalem Wirkungsgrad eingesetzt, d.h. die Separierquote liegt nicht bei 100%
Separierlösungen zur Steigerung der Produktivität
Separiersysteme von MTF Technik leisten einen erheblichen Beitrag zur Verbesserung der Produktivität bei der Herstellung von Spritzguss- oder Druckgussteilen, da sie im Vergleich zur Separation mittels Handling die Zykluszeiten deutlich verkürzen. Daneben amortisieren sich die getätigten Investitionen oftmals bereits innerhalb weniger Wochen.
Ein optimales Ergebnis wird jedoch nur erzielt, wenn die Separiertechnik auch effizient eingesetzt wird. Neben den Parametern Zykluszeit und Kavitätszahl spielt die Geometrie von Nutzteil und Anguss eine entscheidende Rolle. Hier ist grundsätzlich ein gewisser Größenunterschied der Teile notwendig - entweder in der Höhe und/oder in der Fläche.
In unserem Ratgeber finden Sie eine Übersicht über die wichtigsten Gerätetypen mit den jeweils wesentlichen Eigenschaften:
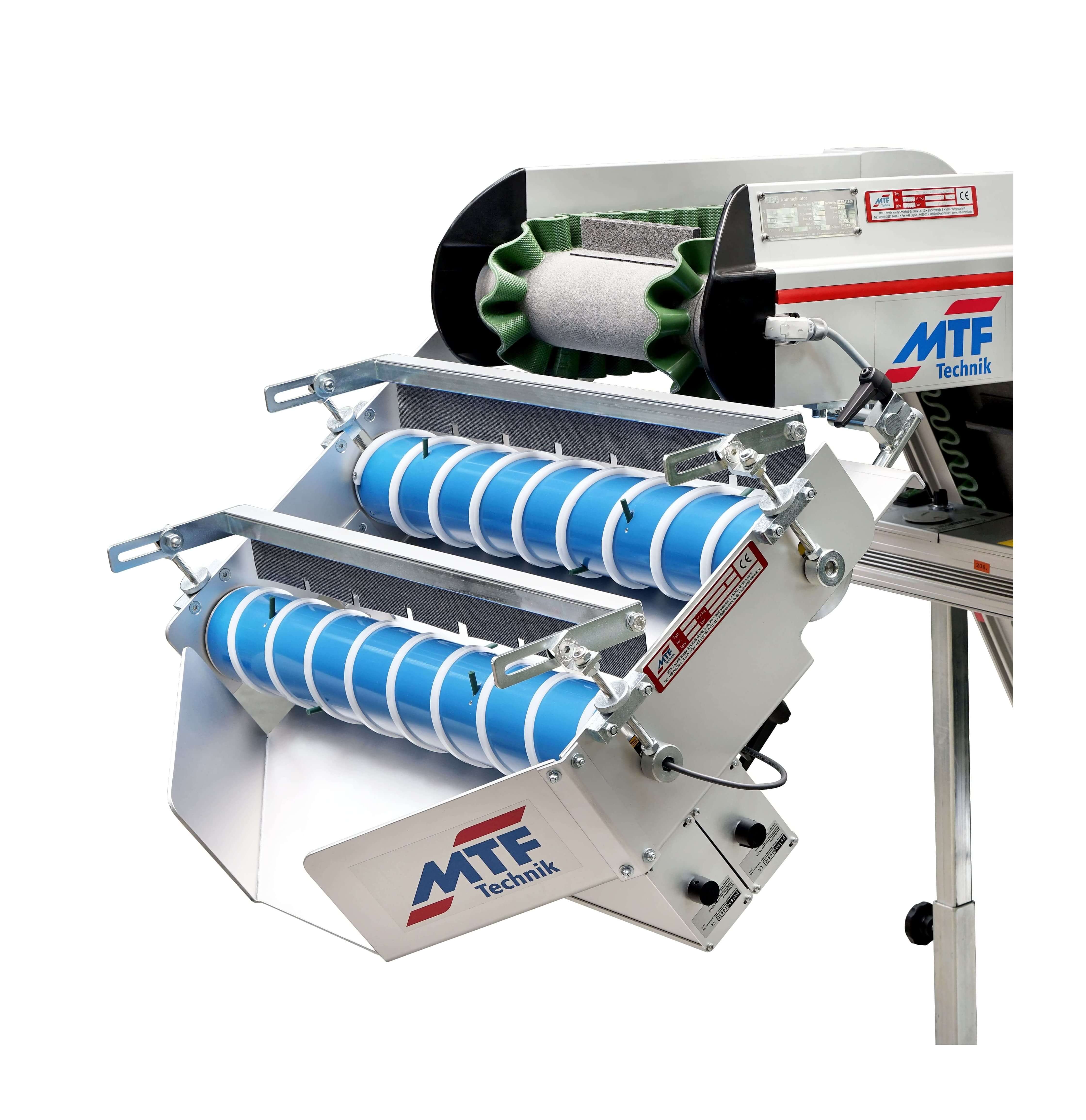
Schneckenseparatoren
Bei den meisten Anwendungen im Kunststoff-Spritzguss führen Schneckenseparatoren zu einem sehr guten Separierergebnis. Die platzsparenden Geräte können als freistehendes Modell (z.B. Multi-Separator MSL 600) oder auch als Anbau am Förderband (z.B. Separator SAL 600) ausgelegt werden.
Hierbei wird eine drehbare Rolle mit einem aufgebrachten Schneckenprofil oberhalb eines fest stehenden Bleches angebracht. Der Separierspalt ergibt sich aus dem Abstand der Schneckenwalze zum Blech, wobei die kleinen Teile unterhalb der Schnecke hindurchrutschen und die großen Teile zur Seite abgeschoben werden.
Um bei diesen Geräten eine optimale Separierquote erreichen zu können, sind einige konstruktive Merkmale wichtig. Wesentlich ist dabei, dass die Schneckenwalze stabil und beidseitig gelagert ist, damit die Walze einen überall gleichen Abstand zum Ablaufblech hat und nicht „eiert“. Darüber hinaus muss die Umdrehungsgeschwindigkeit der Schnecke genau auf die jeweilige Separationsaufgabe eingestellt werden. Einige Bauteile benötigen einen langsameren Separierprozess, andere Teile lassen sich besser separieren, wenn sich die Schneckenwalze möglichst schnell dreht.
Optimal ist in diesem Zusammenhang ein eigener Antrieb der Schnecke mit integrierter Überlastsicherung, um Teileverklemmungen zu verhindern und eine optimale Arbeitssicherheit zu gewährleisten - auch wenn es sich um ein Anbaugerät am Förderband handelt. Somit kann die Umdrehungsgeschwindigkeit der Schnecke unabhängig von der Geschwindigkeit des Zuführbandes geregelt werden. Dies ist insbesondere dann wichtig, wenn die Teile z.B. zunächst auf dem Förderband abkühlen sollen. In diesem Fall sind eine sehr langsame oder getaktete Fördergeschwindigkeit und gleichzeitig eine schnell drehende Schneckenwalze für eine optimale Separierquote notwendig.
Ein weiteres wichtiges Detail sind flexible Stacheln, die entlang des Schneckenumfangs angebracht sein sollten und somit für eine Auflockerung des Separiergutes dienen. Dadurch werden größere Teile, die sich ggf. vor die Schnecke gelegt und den Durchlass für die kleineren Teile versperrt haben, immer wieder in Bewegung gebracht um den Durchlass freizugeben.
Ein flexibler Abstreifer oberhalb der Schneckenwalze verhindert, dass Teile bei der Aufgabe – z.B. durch ein Förderband – über die Schnecke springen. Sie prallen gegen den Abstreifer und werden somit wieder dem Separierprozess zugeführt.
Eine Ausführung für den zweistufigen Separiervorgang ist verfügbar (siehe Foto).
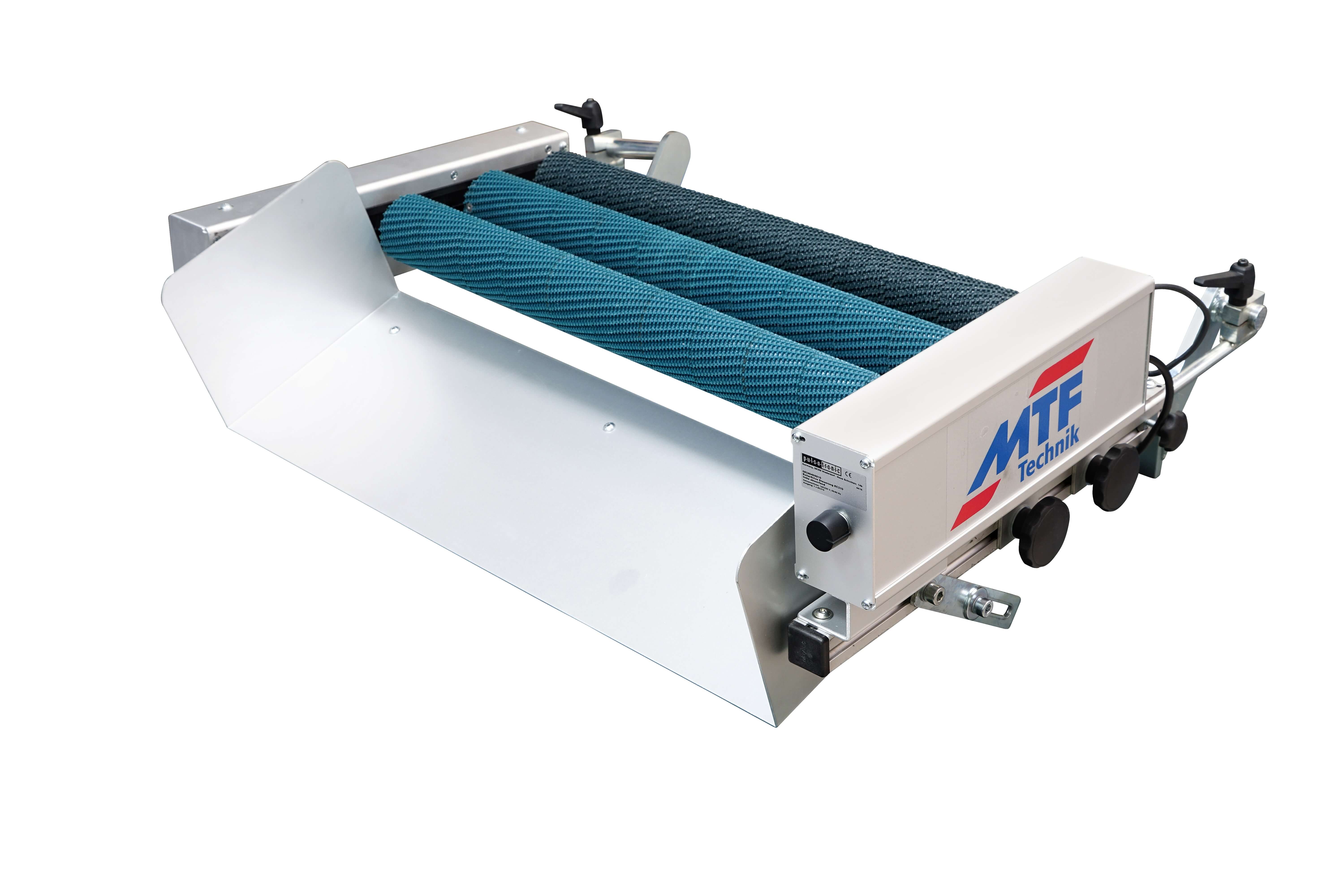
Trennwalzenseparierer
Ein Trennwalzenseparierer, am Auslauf des Förderbands angebaut, eignet sich in vielen Fällen, um Teile und Angüsse mit unterschiedlichen Flächenausdehnungen voneinander zu separieren. Bei diesem Separiervorgang laufen die größeren, flächigen Angüsse über die Rollen hinweg, während die kleinen Teile zwischen den Rollen hindurchfallen. Je nach Art der Bauteile ist es auch auch möglich, einen Scheibenseparierer zu verwenden. Dieser ist als Anbaugerät oder auch als freistehendes Gerät verfügbar.
Wie bei den Schnecken-Separiergeräten steht auch hier vor allen Dingen eine stabile, beidseitige Lagerung der einzelnen Rollen sowie eine individuelle Geschwindigkeitsregelung im Vordergrund, um ein optimales Separierergebnis erreichen zu können.
Darüber hinaus sollten möglichst verschiedene Rollenbeläge eingesetzt werden. Je nach Aufgabenstellung und Teileverhalten kann es nämlich notwendig sein, dass die Rollenbeläge sehr mitnahmefreudig oder glatt sind.
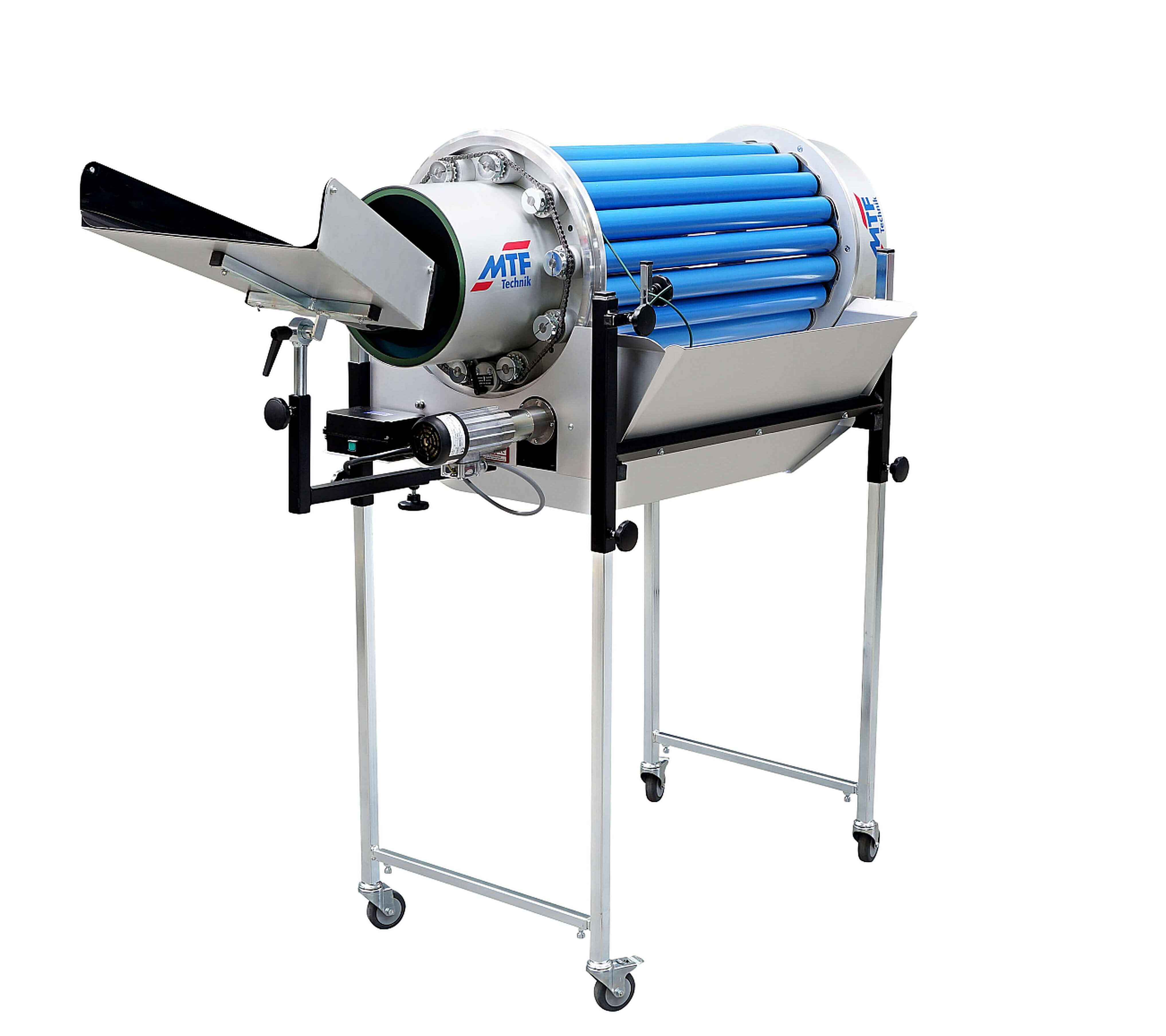
Rollen-Separiertrommeln
Separiertrommeln werden grundsätzlich bei größeren Durchsatzmengen oder Bauteil-Anguss-Kombinationen, bei denen eine Umwälzung zu einer Verbesserung des Separierergebnisses führen kann, eingesetzt. Durch den Umwälzprozess werden verhakte Teile deutlich besser aufgelöst und separiert, als bei den Separiervorsätzen.
Rollen-Separiertrommeln dienen zur Trennung von Bauteilen und Angüssen mit unterschiedlichen Höhenmaßen. Sie können für eine Vielzahl von Separieraufgaben eingesetzt werden. Es gibt Separiertrommeln mit einer Einzelverstellung der Separierspalte oder Geräte mit einer Zentralverstellung (siehe Foto).
Bei der Einzelverstellung wird jede Rolle einzeln im Trommelkäfig fixiert. Der Abstand zwischen zwei Rollen definiert den Separierspalt. Da diese Einstellung verhältnismäßig zeitaufwendig ist, eignet sich eine solche Separiertrommel nur für Anwendungen, bei denen eine Maschine langfristig mit einem Artikel belegt ist bzw. mehrere ähnliche Bauteil-Angusskombinationen mit einer Einstellung getrennt werden können.
Separiertrommeln mit Zentralverstellung der Separierspalte eignen sich hingegen, wenn ein breites Produktspektrum mit Hilfe der Trommel separiert werden soll. Die Zentralverstellung bietet eine schnelle Justierung – sie kann innerhalb weniger Sekunden auf eine neue Produktkombination eingestellt werden. Dabei bilden immer jeweils zwei Rollen ein fest miteinander verbundenes Paar, so dass nur jeder zweite Spalt zwischen den Rollen auch ein Separierspalt ist. Hierdurch reduziert sich die Anzahl der Separierspalte gegenüber einer Separiertrommel mit Einzelverstellung - der maximale Mengendurchsatz ist geringer.
Bei Rollen-Separiertrommeln ist es meistens sinnvoll, wenn die Rollen mittels eines um den Käfig gespannten Riemens angetrieben werden. Hierdurch ergibt sich ein Gegenlauf der Rollen, was Klemmprozesse verhindert. Darüber hinaus wird durch die Drehung der Rollen auch der Separierbereich innerhalb des Trommelkäfigs erhöht. Dadurch wird der Mengendurchsatz und auch die Separierquote gegenüber einem Trommelkäfig mit feststehenden Stäben deutlich erhöht.
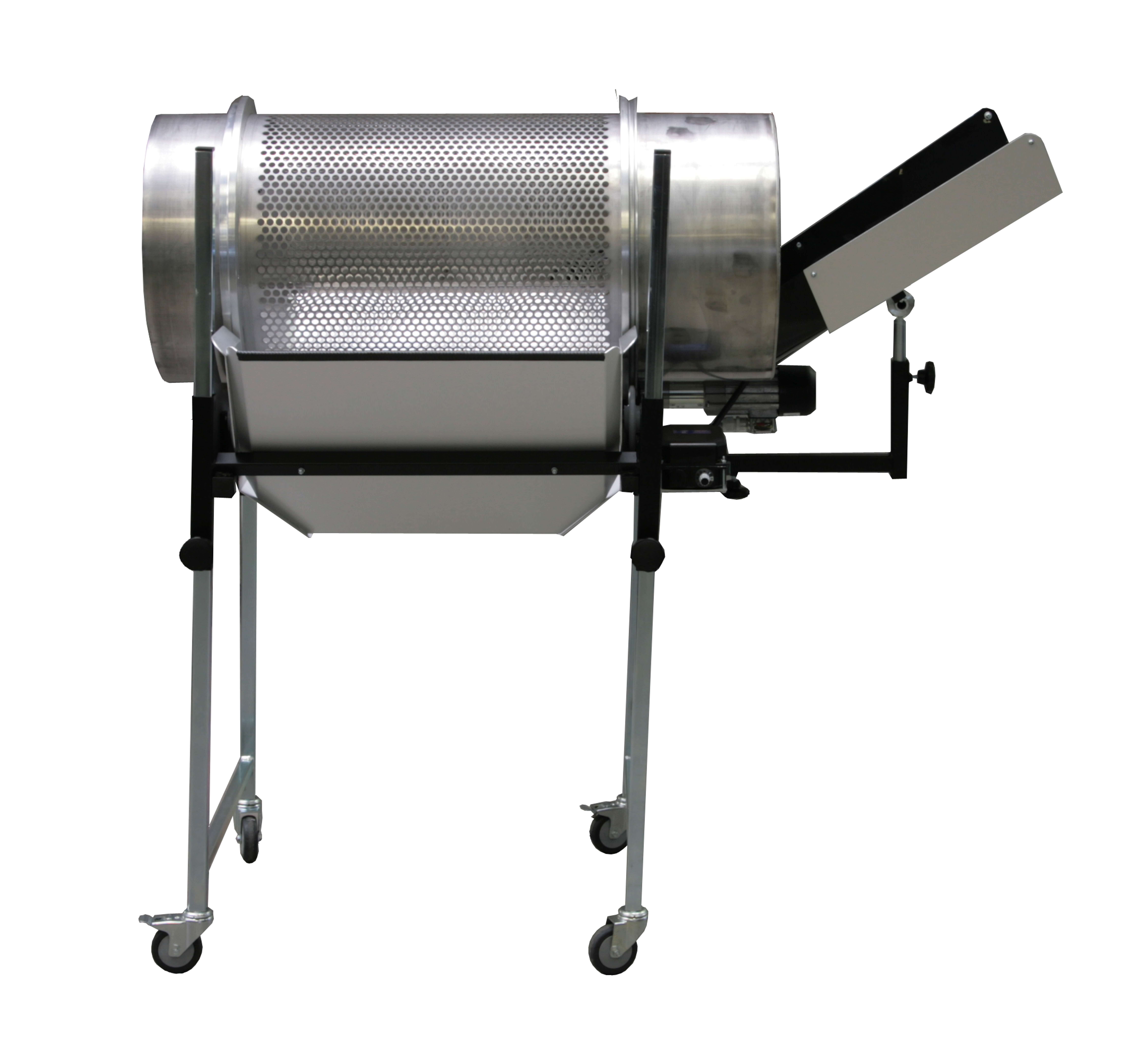
Separiertrommeln mit Lochkäfig
Separiertrommeln mit Lochkäfig kommen dann zum Einsatz, wenn sich die zu trennenden Teile nicht in ihrem Höhenmaß sondern in ihrer Flächenausdehnung unterscheiden (z.B. Münzen mit unterschiedlichem Durchmesser, jedoch gleicher Materialstärke). Der Vorteil der Lochtrommeln besteht zum einen im günstigen Preis, zum anderen in dem großen Mengendurchsatz. Der gesamte Käfig kann mit Löchern versehen werden und wenn die Lochteilung dazu noch sehr klein ist, finden die kleineren Bauteile je Umdrehung viele Gelegenheiten, um aus der Trommel herauszufallen.
Der Nachteil der Lochtrommeln besteht darin, dass die Lochgeometrie fest ist und somit nur auf ein begrenztes Teilespektrum passt. Hier können aber sehr leicht komplette Trommelkäfige ausgetauscht werden, um ein entsprechend größeres Spektrum abzudecken.
Je nach Anwendung kommen bei den Trommelkäfigen viele unterschiedliche Materialien zum Einsatz. Neben Stahl- und Edelstahlkäfigen können hier z.B. Gummi- oder Silikonmaterialien verwendet werden, um eine bestmögliche Teileschonung und auch Geräuschminimierung zu gewährleisten.
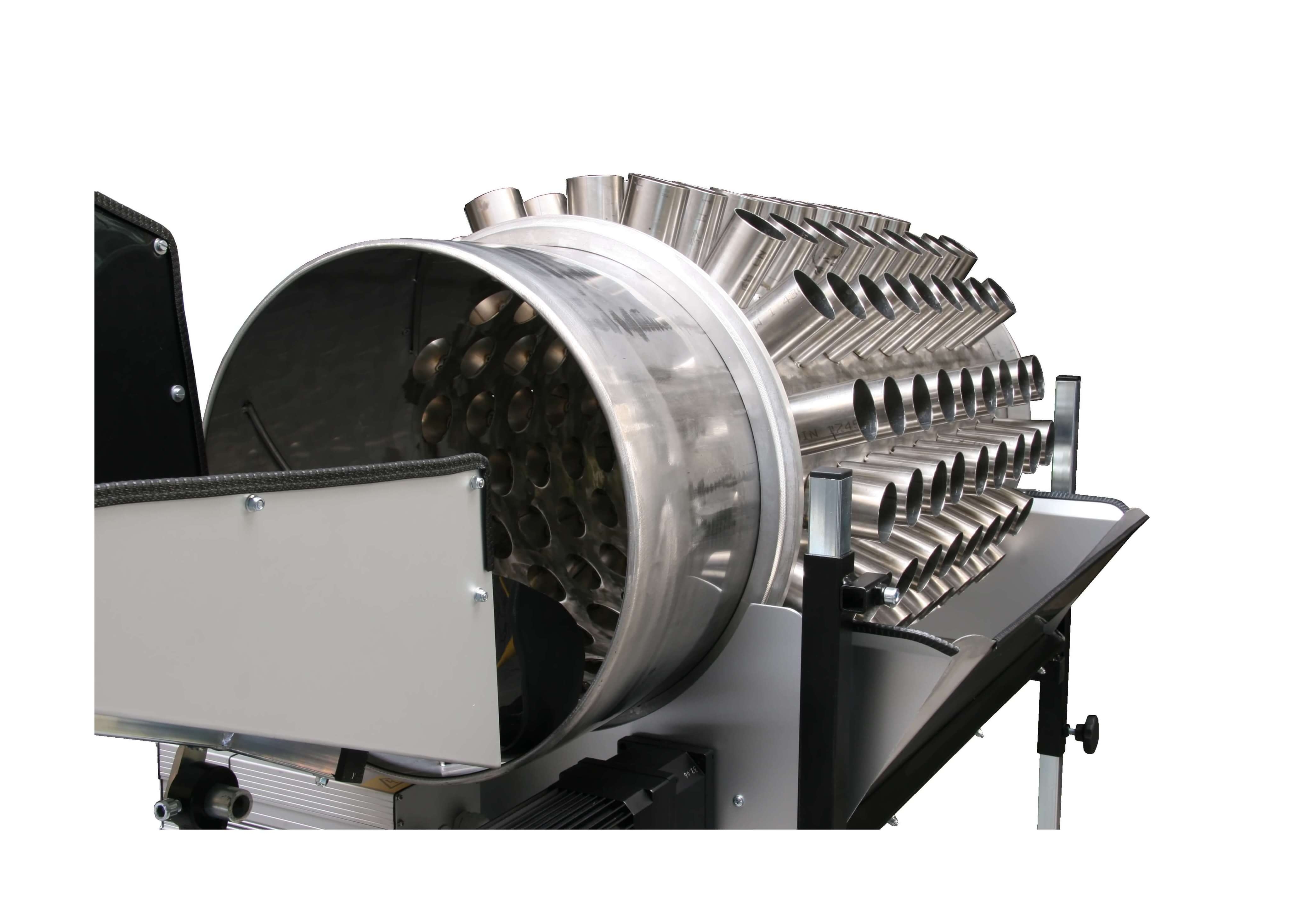
Igel-Separiertrommeln
Igel-Separiertrommeln stellen eine besondere Form der Lochtrommeln für spezielle Teilegeometrien dar. Bei diesem von MTF entwickelten Verfahren werden am äußeren Umfang des Trommelkäfigs in Verlängerung zu den Löchern Hülsenrohre aufgebracht, welche die Geometrie und Größe der Löcher haben. Dies sorgt dafür, dass sich z.B. S-förmige Teile nicht durch die Löcher „schlängeln“ können. Diese Teile können nur mit ihrer Spitze in das Hülsenrohr eintauchen, fallen dann aber wieder zurück in den Trommelkäfig. Ebenso verhindern die Hülsenrohre, dass z.B. verhakungsfreudige Angüsse in den Löchern hängen bleiben können.
Die Käfige sind standardmäßig in Edelstahl ausgeführt (siehe Foto).
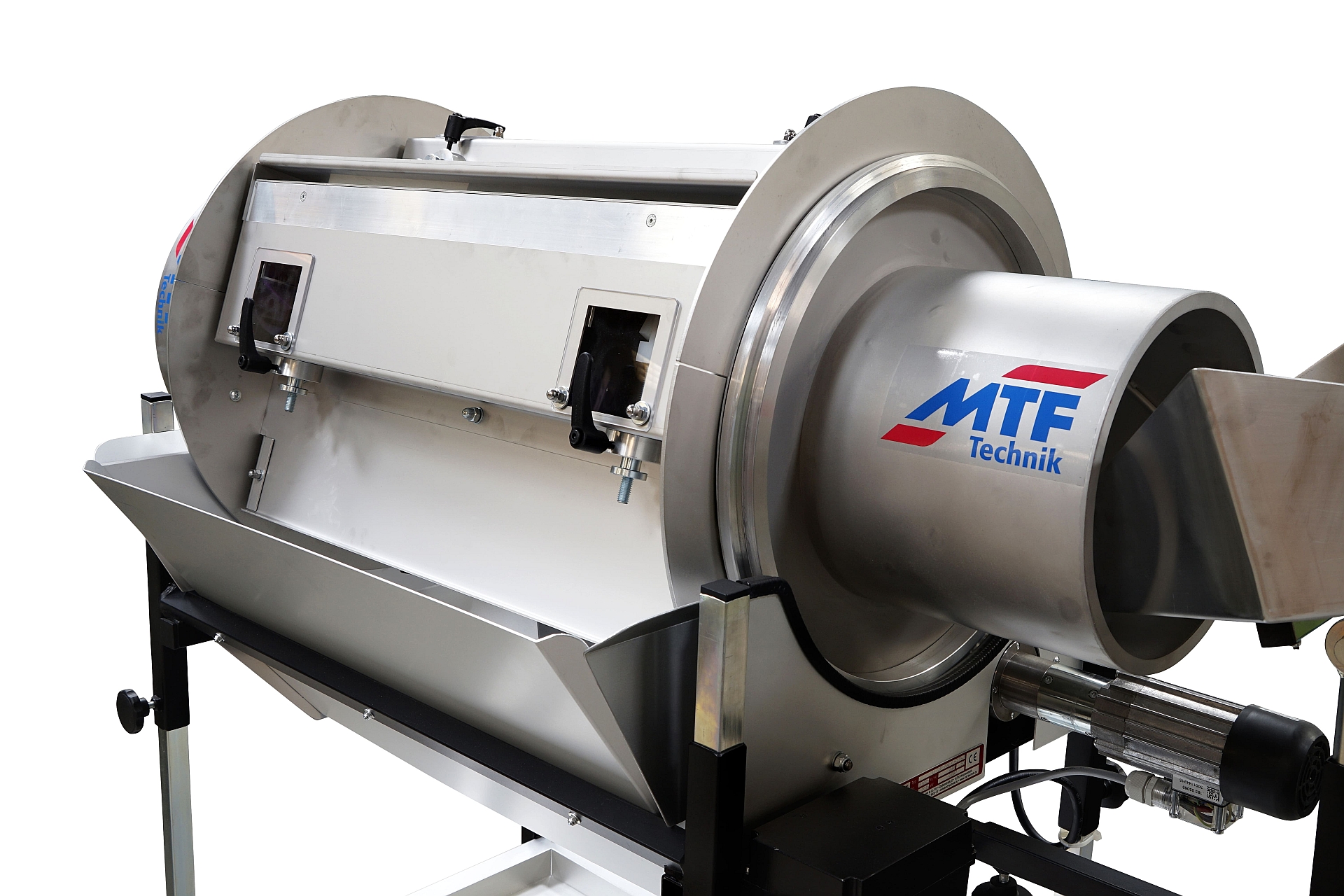
Rechteck-Separiertrommeln
Die Rechtecktrommeln stellen einen komplett eigenständigen Typ Separiertrommel dar und werden meistens bei sehr komplexen Teilegeometrien oder weichen Materialien eingesetzt. Diese Separiertrommeln verfügen über vier Separierspalte, die jeweils aus zwei 80mm breiten parallelen Flächen bestehen. Der Trommelkäfig besteht dabei vollständig aus Edelstahl, so dass die Rechtecktrommeln z.B. auch bei der Produktion von medizintechnischen Artikeln bzw. Reinraumproduktionen zum Einsatz kommen. Die Reinigung der glatten Flächen ist sehr leicht möglich.
Die Separierung erfolgt auch hier – wie bei den Rollensepariertrommeln oder bei Schneckenseparierern – über das Höhenmaß der Bauteile. Die flächenparallele Gestaltung des Separierspaltes verhindert jedoch auch hier ein „Durchschlängeln“ von Bauteilen.
Die Einstellung der Separierspalte erfolgt über Gewindespindeln. Die Höhe des Separierspaltes ist mittels aufgebrachter Maßstäbe exakt einstell- und ablesbar. Somit ist eine hohe Wiederholgenauigkeit gegeben.
Wesentlich bei der Rechtecktrommel ist zudem das von MTF Technik patentierte Verfahren, der sich mit jeder Umdrehung öffnenden Separierspalte. Ein spezieller Mechanismus führt dazu, dass sich die Separierspalte jeweils im oberen Bereich kurzzeitig öffnen. Dadurch können in den Rechtecktrommeln auch Bauteile separiert werden, die sich in anderen Trommeln verklemmen können, wie z.B. sehr kleine oder spitz zulaufende Bauteile. Aber auch sehr weiche Materialien (z.B. Gummi oder Silikon) können in diesem Trommeltyp sehr gut verarbeitet werden.
Haben Sie weitere Fragen? Wir stehen für Sie jederzeit telefonisch unter +49 2261 9431-0 oder info@mtf-technik.de zur Verfügung oder benutzen Sie unser Kontaktformular.